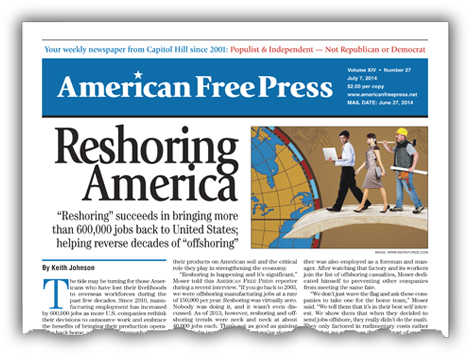
• “Reshoring” succeeds in bringing more than 600,000 jobs back to United States; helping reverse decades of “offshoring.”
By Keith Johnson —
The tide may be turning for those Americans who have lost their livelihoods to overseas workforces during the past few decades. Since 2010, manufacturing employment has increased by 600,000 jobs as more American companies rethink their decisions to outsource work and embrace the benefits of bringing their production operations back home, a trend now commonly referred to as “reshoring.”
Leading the way to this new era is Harry Moser, founder and president of the Reshoring Initiative, an industry-led effort that helps United States manufacturers realize the advantages of making their products on American soil and the critical role they play in strengthening the economy.
“Reshoring is happening and it’s significant,” Moser told this AMERICAN FREE PRESS reporter during a recent interview. “If you go back to 2003, we were offshoring manufacturing jobs at a rate of 150,000 per year. Reshoring was virtually zero. Nobody was doing it, and it wasn’t even discussed. As of 2013, however, reshoring and offshoring trends were neck and neck at about 40,000 jobs each. That’s not as good as gaining 150,000 jobs per year, but at least we’ve stopped the bleeding.”
For Moser, the mass exodus of U.S. jobs is something that hits close to home. As a teen, he worked summers at the once sprawling Singer Sewing Company in Elizabeth, New Jersey, where his father was also employed as a foreman and manager. After watching that factory and its workers join the list of offshoring casualties, Moser dedicated himself to preventing other companies from meeting the same fate.
“We don’t just wave the flag and ask these companies to take one for the home team,” Moser said. “We tell them that it’s in their best self interests. We show them that when they decided to send jobs offshore, they really didn’t do the math. They only factored in rudimentary costs rather than what we refer to as the ‘total cost of ownership,’ which includes duty, freight, packaging, carrying costs of inventory, travel expenses to check on suppliers, intellectual property risk and the impact on innovation when you separate engineering from manufacturing. There are 29 factors we use to help companies calculate their actual offshoring costs in hopes they’ll be more objective in their decision making.”
Moser told AFP that the ever changing work environment at foreign factories is slowly reversing the trend of exporting U.S. jobs.
“When you do the math you’ll find maybe 25% of the cases where the work should be brought back right now,” said Moser. “But as Chinese wages continue to go up at a rate of about 15%-18% per year, it will start making sense for a lot more companies to bring those jobs home.”
Quality of workmanship is also a factor compelling some U.S. compares to reshore.
“I was at a [June 17] reshoring conference at the Congressional Visitors Center, where one of the speakers reported that the rate of recalls on Chinese products is six times as high as on American products,” Moser said. “The general belief, in many industries, is that [foreign factories]
tend to do a good job cranking out high volume products, such as electronics, while the quality of their tooling and mold work is not nearly as good as it is in the States.”
When asked if there really is high demand for U.S. products, Moser replied: “We have 12 independent surveys about consumer preference and the conclusion is that Midwesterners, older people and the affluent prefer to buy American and will pay somewhat more for it. People also say they will pay more for U.S.-made safety related products, such as the buckle for your parachute or the material used to make your child’s crib. I believe that if a ‘made in America’ product is easy to find, most consumers will buy it, and I’ve been working with retailers to help make that happen.”
Moser went on to say that his biggest challenge in meeting this emerging demand is the lack of a skilled workforce.
“Our basic education system isn’t good enough, and it’s not providing the right incentives,” he said. “Too many [here] want to be in front of a camera or behind a microphone, and too few want to be a toolmaker or welder. The Germans and Swiss place a higher value on these professions. That’s why their people are making a third more than ours and have a trade surplus instead of a trade deficit.”
Motorola, Whirlpool and Caterpillar are just a few of the big name corporations that have decided to bring at least part of their production operations back to the U.S.
“The reshoring trends are [strongest] in electronics, computers and, surprisingly, apparel,” Moser said. “Apparel is fourth on the list and the last thing you think would come back because it’s so labor intensive. That’s if you look at the number of companies. If you look at the number of jobs, which I think is a lot more important, it’s appliances and machinery, because if Caterpillar puts in a factory that equates to a couple thousand jobs where the apparel cases are three here or four there. It’s good these companies are coming back but it’s the jobs they bring with them that really count.”
Keith Johnson is a writer based in Tennessee. He can be contacted at keithj.americanfreepress@yahoo.com.